Ever wondered how Helix, Titan and Leesa mattresses are made? We visited a factory to see the process in action
A step-by-step guide to how your mattress is made
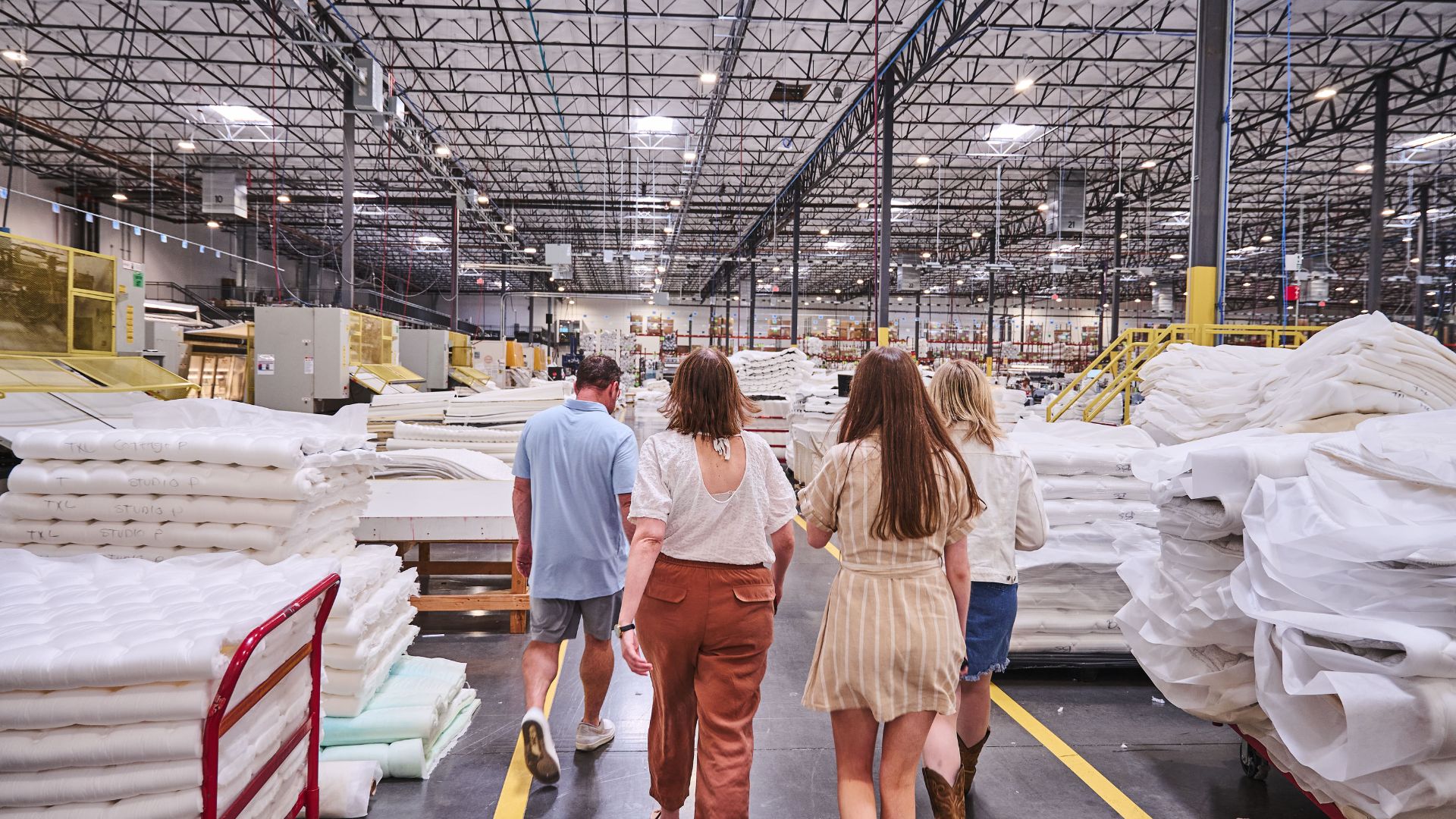
Since becoming sleep writers here at Tom’s Guide, we talk a lot about mattresses. From reviewing the latest beds and the biggest sales of the year at the most well-known sleep brands, we’ve picked up a lot of mattress knowledge. However, we had never actually seen the making of a mattress.
That’s why when mattress manufacturer 3Z Brands offered us the opportunity to visit their factory in Arizona, we jumped at the chance. After all, the factory is where some of this year’s best mattresses are created, including beds from Helix, Leesa, Brooklyn Bedding, and Nolah.
The tour was guided by none other than the CEO of 3Z Brands, John Merwin, and we had the chance to pick his brains about the mattress-making process. Read on to discover the steps needed to make a high-quality mattress and our thoughts on the tour. And with the Cyber Monday mattress deals arriving tomorrow, what better time to find out how the mattresses on your wishlist are made?
What mattresses do 3Z brands make?
3Z Brands is the parent company behind world-class sleep brands such as Nolah, Bear Mattress, Brooklyn Bedding, Helix, and Leesa. The company prides itself on its high-quality US-made mattresses, and every bed produced by the business is GREENGUARD Gold-certified and free of fiberglass.
Where are 3Z mattresses made?
All of the mattresses manufactured by 3Z Brands are American-made in the company’s factory found in Phoenix, Arizona. The factory is just two-and-a-half years old, with the doors opening in early 2022.
This new, larger site means they can make all the components of a mattress under one roof. In-house production allows more leeway for experimentation and to respond quickly to any concerns or customer interest.
A step-by-step guide to how mattresses are made
1. Foam pouring, setting, and cutting
Our first stop on the factory tour was the foam section. Foam is found in pretty much all of the mattresses created here as it’s a key ingredient of both all-foam and hybrid beds. So this is a fitting place to start.
Sign up to get the BEST of Tom's Guide direct to your inbox.
Get instant access to breaking news, the hottest reviews, great deals and helpful tips.
The mattress foam begins its life as liquid, which we then got to see being poured into an intimidatingly huge foaming machine. As the machine makes around 25 different types of foam, an advanced computer system controls all the variables needed to make each specific foam.
In fact, we were told by 3Z’s foam chemist Neil Silverman that producing foam is a lot like making a cake or a bun; the foaming machine acts as the oven, while the computer system is the recipe book telling the machine which ingredients it needs to make it.
Once the foaming liquid is poured into the machine, it then goes down a conveyor until it resembles a white, viscous river. As it makes its way through the line, the liquid expands and rises into foam.
By the time the foam comes out of the line, it has expanded to whatever size it needs to be, with the computer setting the width on the machine and a blade cutting it into large blocks. When the foam emerges, it no longer resembles the thick goo that was poured into it. It now resembles 7ft marshmallows.
During the tour, CEO John Merwin placed his hand on one of the foam blocks, and told us how sticky and warm it still is from the chemical reaction. The machine, if run non-stop, is capable of making 8,000 queen-sized all-foam mattresses in just eight hours. ”Obviously, we don’t make that many beds in a day,” said John, “But hopefully, someday we get to that point.”
Just as buns need to cool, the foam then needs to set. These blocks of foam are placed in bays for at least 72 hours to set and cool down, and are then cut down even further. When cut, any unwanted foam is then recycled and remade into carpets or shredded into filling for foam pillows, which is a great way to eliminate waste.
2. Wire coiling
The vast majority of mattresses by 3Z are hybrids, which means they contain both foams and springs. (Although 3Z does manufacture some all-foam beds, such as the Plank Firm mattress we got hands-on with). And as with the foams, these coil layers are also made in-house.
It all begins with a big spool of wire. The wire is fed into a coiling machine, where it’s heated to add strength and spun into a coil. Each machine can make a maximum of 160 coils per minute. The one we watched has racked up 26 million coils in its lifetime — that’s a lot of beds.
Once cool, the coil is compressed into a fabric pocket. This compression, sometimes reducing an 11-inch coil down to eight inches, enhances the responsive support you’d expect from the best hybrid mattresses. Every coil is placed in a pocket, with each pocket attached to form a ribbon of springs.
These ribbons then pass through the assembly machine, where they’re glued into rows to create the base of your hybrid mattress. Stronger coils are often used around the perimeter to enhance edge support, and you’ll also find these stronger coils in the center of a mattress with enhanced lumbar support.
During our visit, the factory was on the cusp of manufacturing its own micro coils. Until now, these have been shipped in, but they’re set to be made on-site. The process is very similar, except the micro coils, as the name suggests, are made much smaller.
3. Sewing and quilting
The final ingredient of the mattress is the cover, which at 3Z is also constructed in-factory. The fabric is, however, made off-site. That includes any materials with added properties, such as the cooling GlacioTex covers you’ll find on some Helix mattresses, or the celliant-infused covers available for Bear mattresses.
The quilting takes place on what’s essentially a massive sewing machine. Combining the fabric cover with a layer of foam, this quilting adds an immediate plush comfort to the mattress. And the quilting pattern is more than just a pretty finish — it can affect the overall feel. A cover with a continuous tight pattern has a firmer finish, while a looser pattern gives a softer feel.
The covers are then passed onto the sewing team, to neatly finish the borders. “Everyone that visits here is always a little bit surprised at the level of hands-on work that we still run on,” John explained, but it’s these team members that give your 3Z mattress its final polished look.
And it’s a very tricky part of the process, as we discovered when one of the Tom’s Guide team tried their hand at sewing. Our scrap border wouldn’t be good enough for a dog bed (don’t worry, it went into the recycling pile).
This is also where the sides of the bed are made, plus any aesthetic touches are added, including handles. Handles are apparently a bit of a “bottleneck” in the process, which is why you don’t see them on every bed — although we always appreciate them.
4. Lamination and assembly
With every layer crafted, it’s time to put the mattress together. It starts with the lamination process, where each foam and coil layer is glued into place. Like many steps of the process, this was unexpectedly hands-on. As John explained, “to make sure you do a good enough job to square things up, you have to have some hands working on it”.
Each layer is stacked, glued, aligned, and lightly compressed to activate the glue. Every mattress in the factory goes through the process, so things could get confusing, but there’s no risk of a bad build. “These guys [at the lamination machine] are well versed, so it doesn’t matter what we send down the line,” says John. “They know every bed in here.” (And RFID helps keep things running smoothly.)
After lamination, it’s time to add the covers. The top, base, and sides are all stapled to the mattress, creating the bed that you’ll sleep on at home.
This is also the final opportunity for quality checks. John explained that an advantage of in-house manufacturing is that quality checks are performed at every step of this process. By this point, it’s a simple once over to make sure everything is as it should be. If it’s not good enough, the mattress will be pulled off.
And these final checks are necessary, as the next person to see the mattress in its finished state is the owner. Because now, it gets flattened, sealed, and rolled…
5. Rolling and packing
Once the mattresses are fully assembled, they need to be flattened, sealed in plastic, rolled, and then packed into a delivery box. While traditional mattresses are either sold in stores (or delivered and installed) flat, this factory produces some of this year’s best mattresses in a box. This means that all 3Z brand mattresses are compressed with a heavy weight (around 60 tons), rolled in plastic, and placed in a box for a quick and easy delivery.
The compress-and-roll-process is a delicate one. If you try to compress too many mattresses too quickly, apply too much force, or compress a mattress size that’s too big, it can damage both the compression machine and the mattress. (A mistake John admitted to making when he first entered the bed-in-a-box game and boxed mattresses were still a novelty.)
To avoid damage, the rolling and packing is broken down into steps. First the mattress is flattened (mattresses can be flattened here every 27 seconds) and condensed, before entering the rolling cage.
Once the mattress is rolled and secured in its 3.5mm plastic wrap, they are then boxed into their brand’s unique packaging, from Helix to Leesa. The box is then marked with a delivery address label and ready to be shipped to doorsteps across America.
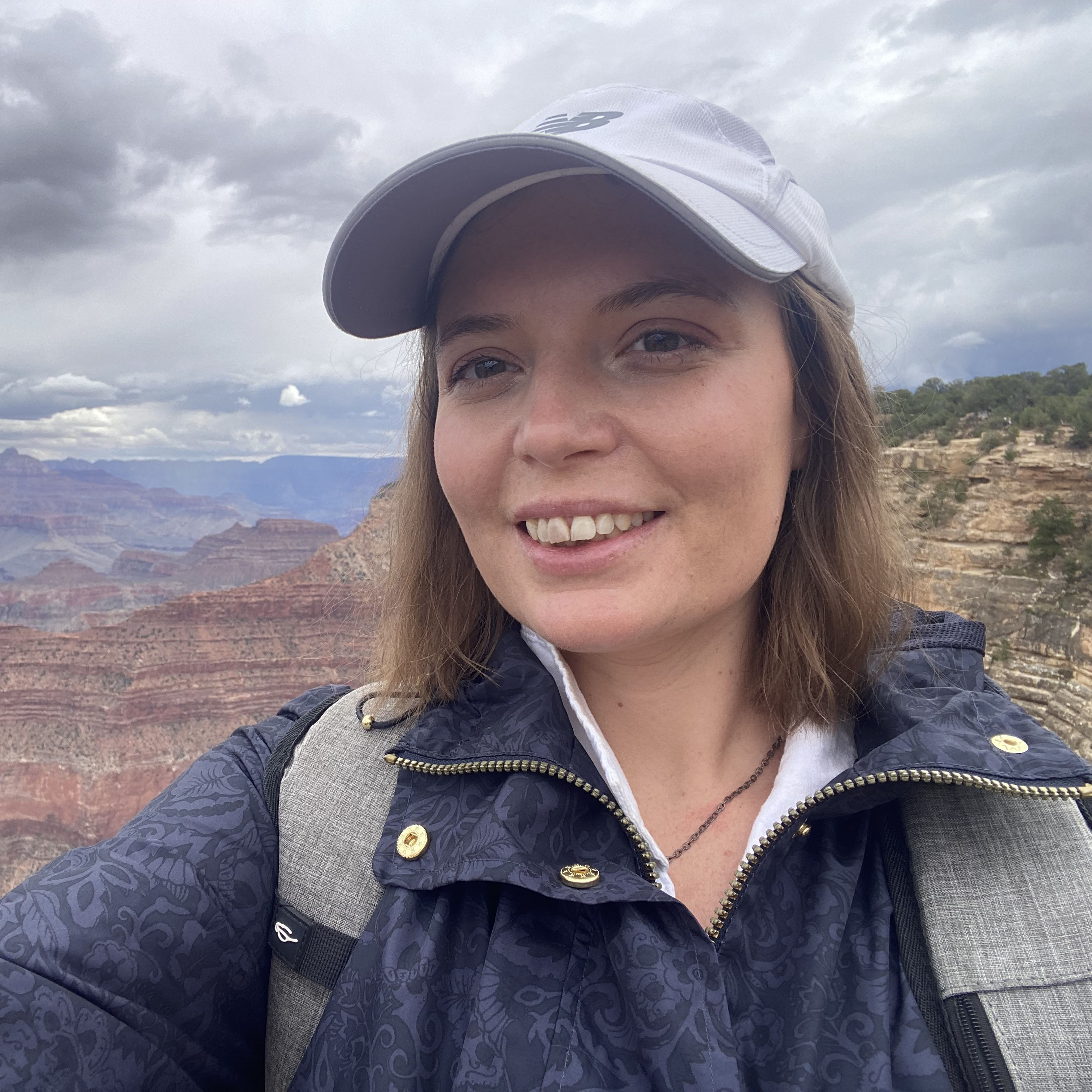
Ruth is a staff writer at Tom’s Guide, covering all things mattress and sleep. She has a deep interest in the link between sleep and health, and has tried enough mattresses to know the right bed really can make a difference to your wellbeing. At Tom’s Guide she writes to help people sleep better, from how-tos to the latest deals to mattress reviews, and has interviewed an array of specialists who share her passion. Before joining the team at Tom’s Guide, Ruth worked as a sleep and mattress writer for our sister website, TechRadar.