Forget Plastic: Molten Metal 3D Printers Are Coming
Father-son team has developed a printer that squirts out droplets of molten metal, similar to how a desktop printer spits out ink.
Home 3D printers such as the Cubify Cube and MakerBot Replicator build objects by laying down layers of melted plastic filament. They've inspired a wave of creativity by allowing people to transform an idea into an original, custom-designed object. But still, it's a piece of plastic — good for industrial prototypes or low-cost toys, tools or tchotchkes, but not for precise parts or polished, durable items.
Father-and-son team Scott and Zachary Vader aim to take 3D printing up a substantial notch by printing with molten metals such as aluminum and copper. In rough terms, their prototype machine, which debuted at Maker Faire in New York City over the weekend, is like an inkjet printer for metal.
MORE: 10 Great 3D Printing Projects
You may not have one of their machines at home soon, or ever, though: The first units, to be called the Mark 1, will be custom-built works in progress and likely sell for between $20,000 and $100,000. But they could make many of the components in the products you buy and the machines that make those products, the inventors say. The Vaders intend to come out with a version under $10,000 in about a year, son Zachary Vader told Tom's Guide. "But at this point we don't have any idea of what that will be or look like."
In the future, the printers could allow "maker" inventors to build their own dream machines in small workshops. "I think in a few years this could be a maker product, a tool that a maker space might have for its members," Scott Vader, the father, said. (Their website, Vadersystems.com, waxes more poetic, reading "… our Direct to Metal printer will be not only be a tool of the corporate world, but also of the common man.")
Metal printing state of the art
Metal printing is possible now, but not for heavy-duty industrial parts. The most common process, selective laser sintering, lays down a layer of metal powder and heats it with a laser so that the metal melts and flows together. It's increasingly used to produce items such as jewelry that you can buy on sites such as Etsy. But the objects aren't ideal for building machine parts because they are slightly porous, Zachary Vader said.
MORE: Best 3D Printers 2013
Sign up to get the BEST of Tom's Guide direct to your inbox.
Get instant access to breaking news, the hottest reviews, great deals and helpful tips.
So the Vaders are going a different route — one that looks more than any other technology like the inkjet printers that inspired 3D printing in the first place. The startup's printer process begins with an electric furnace up top that melts metal ingots. That process is quite energy efficient. The printer runs off a regular wall outlet: Its 400-watt power supply would barely power a desktop computer. The furnace is encased in a glossy-black cube with the family name imprinted in bold, angular letters on the front — calling up the aesthetic of a more-famous Vader.
Zachary Vader, 20, who has studied mechanical engineering, was reticent to explain exactly how the family's technology works. But in broad terms, he said that the process — called liquid metal jet printing or direct-to-metal printing — uses magnetism to propel melted metal onto the printer bed. Some metals already have magnetic properties. For others, like the aluminum the machine will first support, the printer first has to apply an electrical charge to the metal.
That mechanism closely resembles some inkjet printers, which apply an electrical charge to droplets of ink and use magnetic force to direct them onto a sheet of paper. Rather than squirting out one drop at a time, even cheap inkjet printers can propel them through thousands of nozzles, thousands of times per second. Zachary Vader said that their device can likewise have thousands of nozzles and run close to or even faster than the speed of an inkjet. Today's plastic printers typically have just one nozzle, and at most about a half dozen, that trace out a design.
Because the electrical conductivity of the metal is key to the printing mechanism, adding new materials may require some tweaking of the process, Zachary Vader said. But he believes copper, silver and gold will be fairly easy to add.
The Vaders still have a way to go, however. They finished putting the prototype together a few days before the New York debut. And it was missing the most important part: the printhead. Nor did the team display any items made with its printer.
How metal printing makes a difference
What's the point of printing metal other than "because we can"? First, there's the generic benefit of 3D printing — it can make a single, unique object that previously could only be mass-manufactured. That would allow companies to build a small number of products or prototypes, such as 100, or even just 10. And it could drop the cost of making one-off, custom metal items, such as prosthetics or medical implants, Scott Vader said.
But metal printing could also create new types of lightweight metal components. Rather than producing solid pieces of plastic, 3D printers typically print out a honeycomb-like internal structure to save on weight and material. The Vader printer can do the same thing with metal.
"What you could do that would be even cooler than a gear is you could do a gear that is hollow inside that has specific support structures for the direction of torque," the younger Vader said, "so it can be very, very light, and [have] very, very low material costs, but do the job extremely well."
For all those reasons, Scott Vader is upbeat that metal printing will go big. "It could be one-third of the manufacturing world someday," he said. "Of course, I'm being optimistic," he added
Follow Sean Captain @seancaptain and on Google+. Follow us @tomsguide, on Facebook and on Google+.
Sean Captain is a freelance technology and science writer, editor and photographer. At Tom's Guide, he has reviewed cameras, including most of Sony's Alpha A6000-series mirrorless cameras, as well as other photography-related content. He has also written for Fast Company, The New York Times, The Wall Street Journal, and Wired.
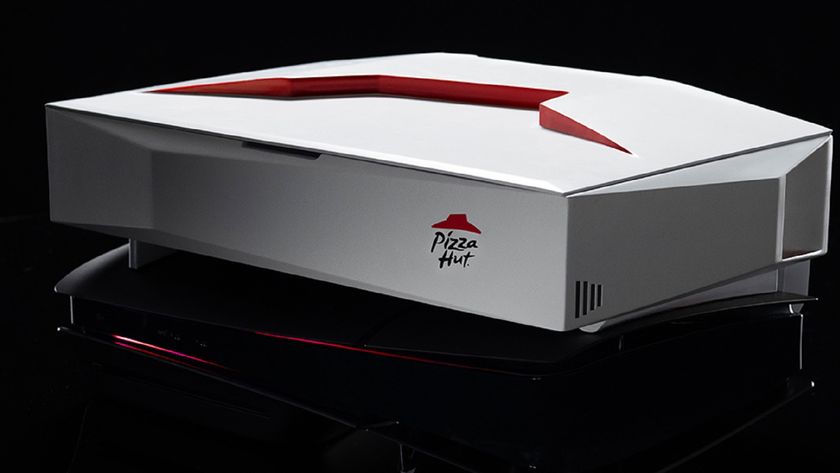
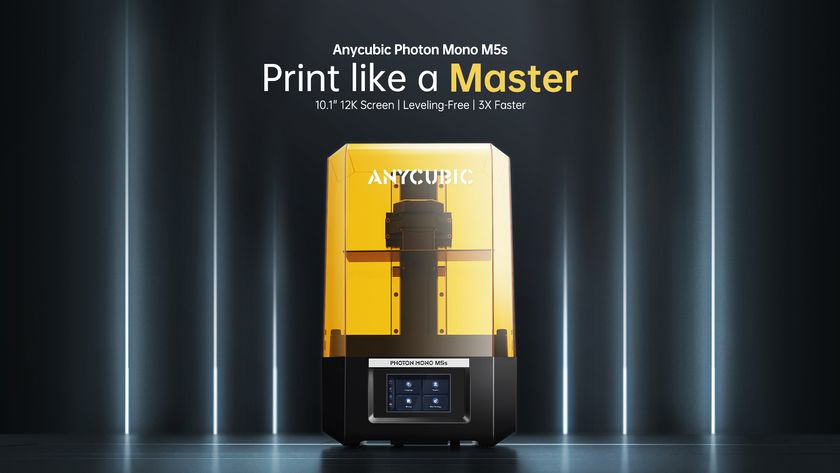
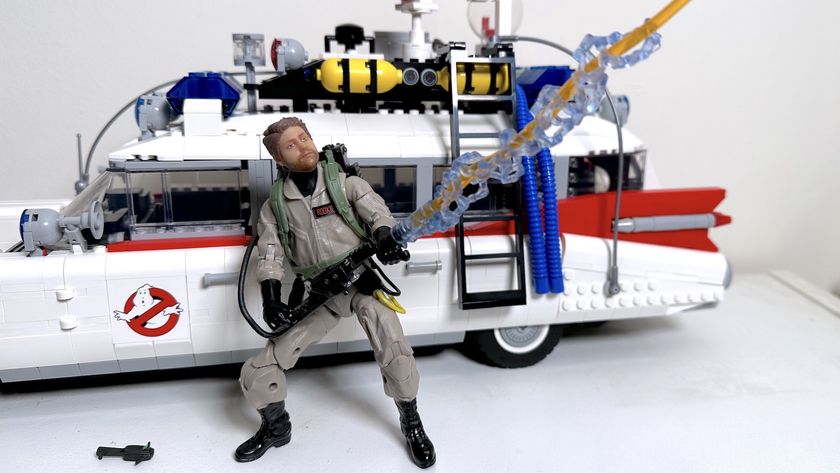
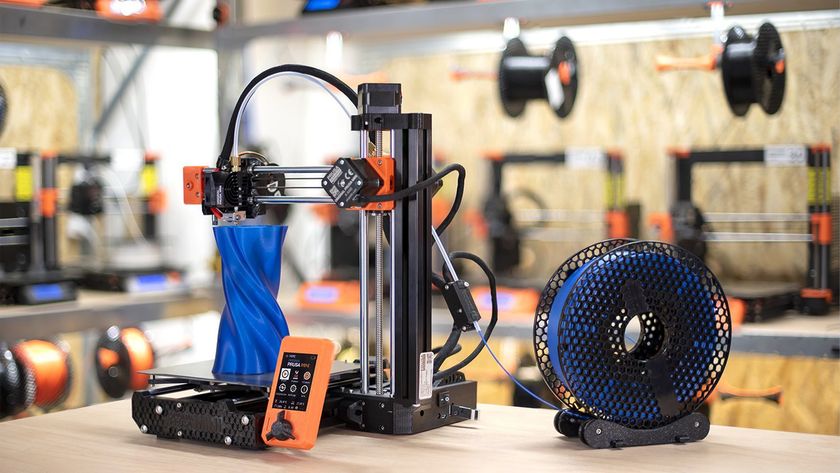
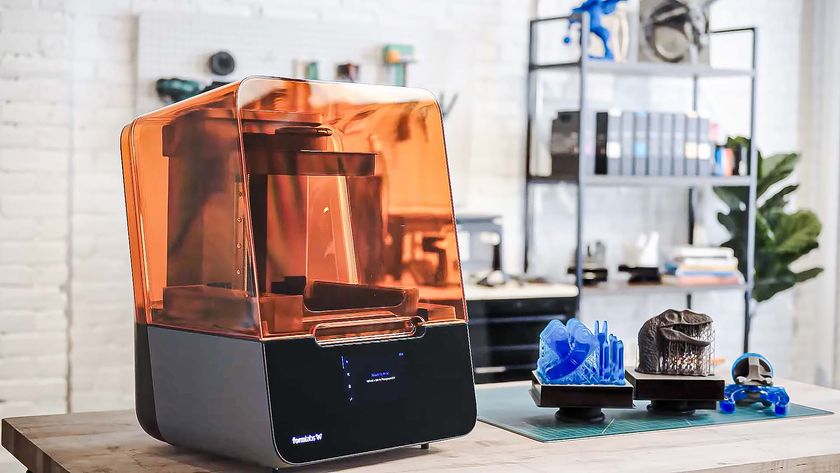
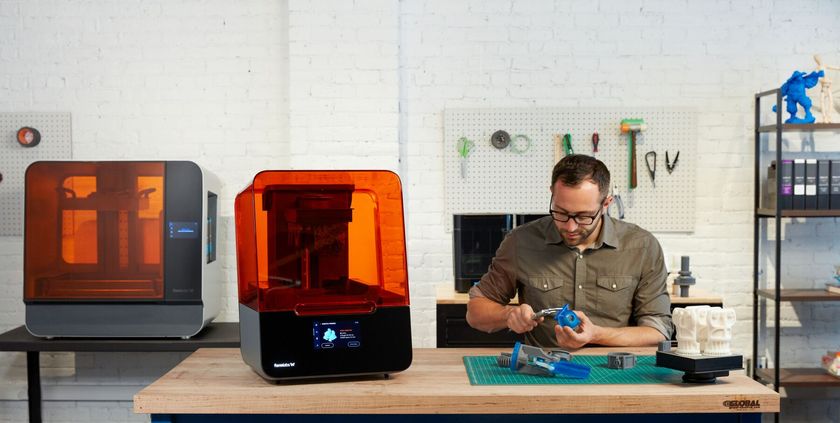
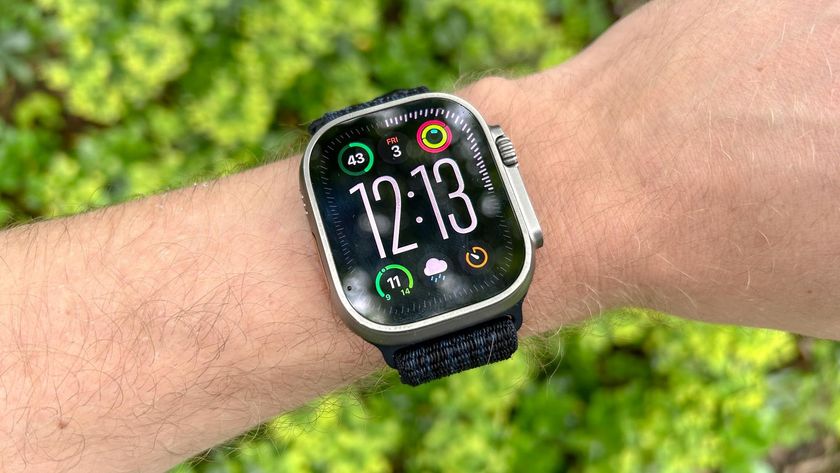
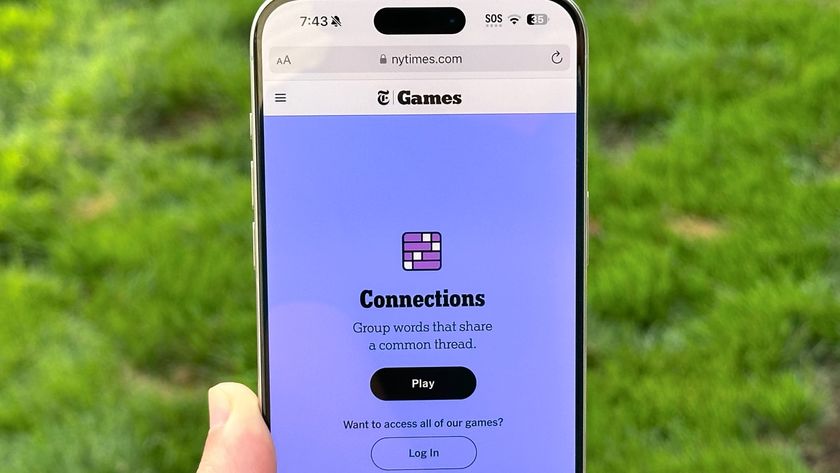
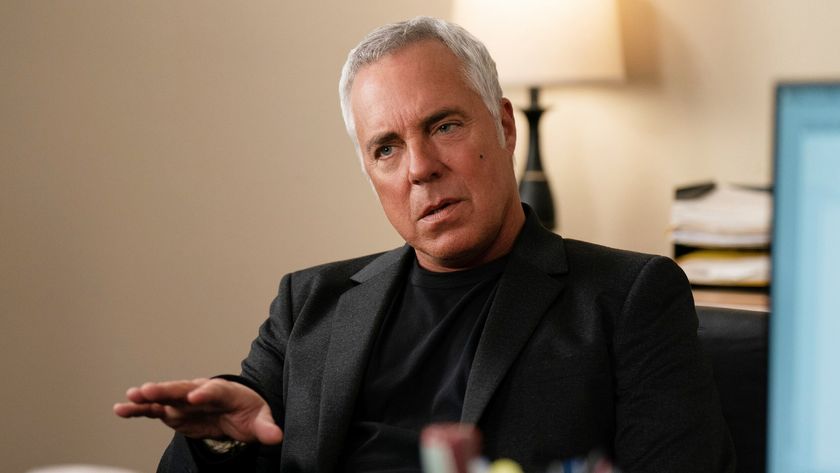
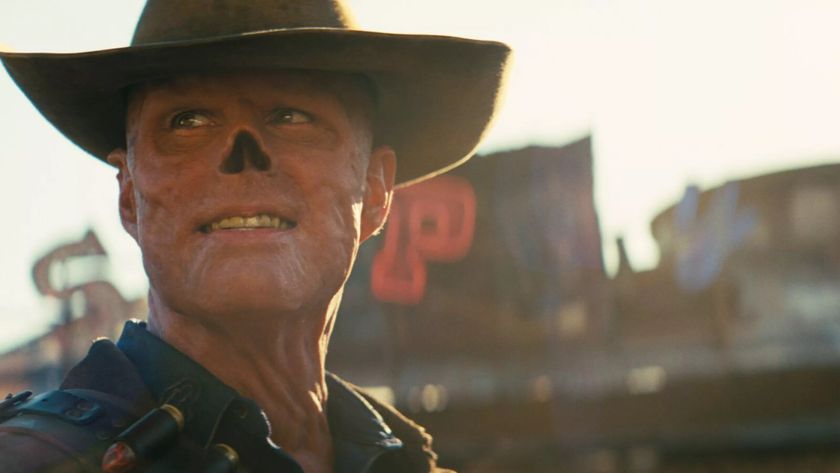
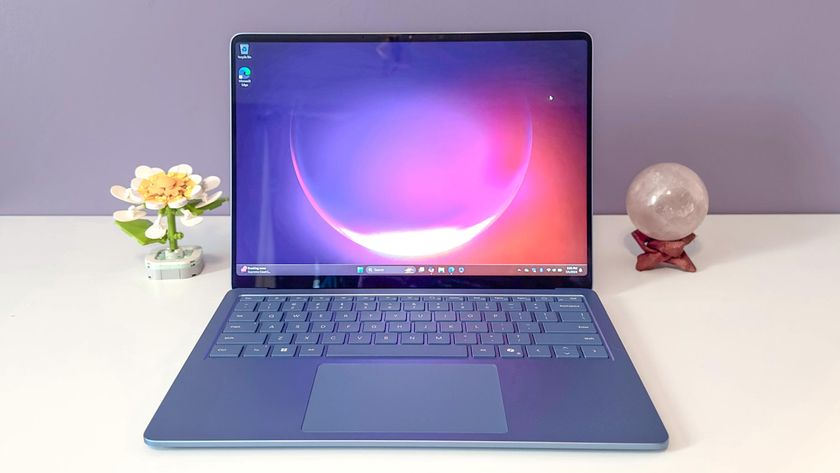
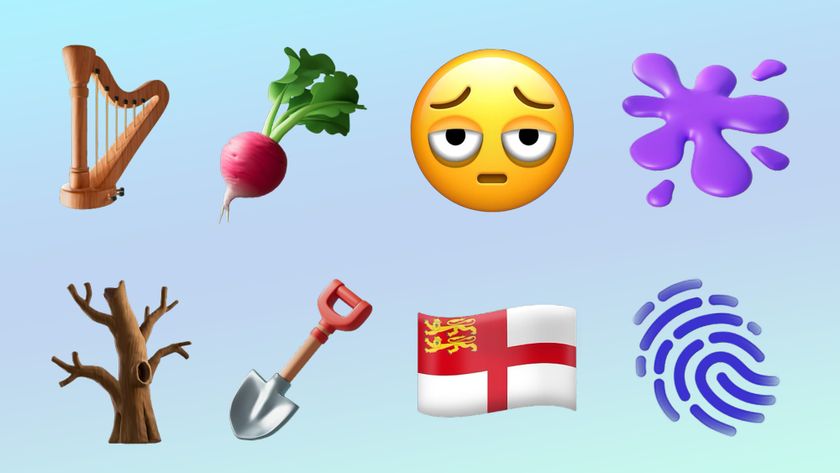
-
chicofehr I want to print a solid metal case for my phone and take the guts out and put it in it. OK that might be weird but I would try it if I could.Reply -
Spooderman This is really cool and could be incredibly useful if the price comes down enough. However, I assume that metal for the machine to consume will be pretty pricey.Reply -
TeraMedia Every hardware store in the world worth the parking lot it sits next to should have one of these, connected to an online special parts catalog.Reply -
Narcissistic_Martyr I can see some use for making bespoke titanium medical implants and the like but I'm sure that people will find a ton of great ways to use the technology once it exists.Reply
However, the big problem I see is that you won't be able to print many alloys (like steel) very well because the material properties of metal alloys are highly dependent on how you cool the molten metal.
-
noob2222 doing the transfer from the melting pot to the print head is going to be the tough part. copper is melted at ~1000c. The print head itself would have to maintain that temperature in order to keep it from becoming a solid again. The object being made must also be cooled at an even rate or it will warp, especially with soft metals such as aluminum. In order to make anything from steel, the print head would likely need to be tungsten. Another difficulty is going to be keeping the molten metal from oxidizing.Reply
Nasa is working on SLM (selective laser melting) for this type of project. (sls on steroieds)
One thing about it, using it in winter time will cut down on heating costs :) -
coovargo @cos2012Reply
Zachary Vader, 20, who has studied mechanical engineering, was reticent to explain exactly how the family's technology works. But in broad terms, he said that the process — called liquid metal jet printing or direct-to-metal printing — uses magnetism to propel melted metal onto the printer bed. Some metals already have magnetic properties. For others, like the aluminum the machine will first support, the printer first has to apply an electrical charge to the metal.
Read much?