From idea to final form, SLA 3D printers have some significant advantages over FDM
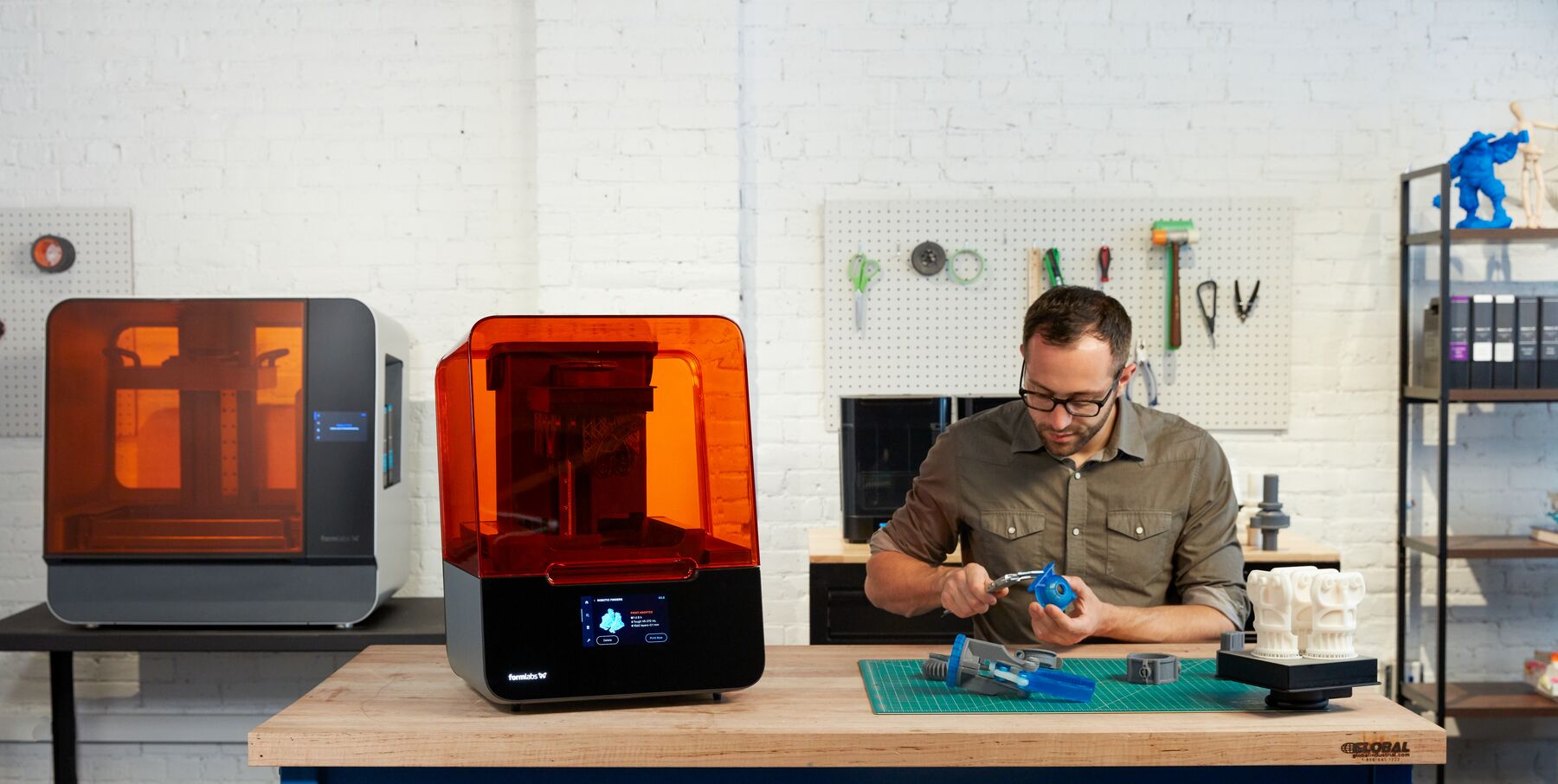
For the month of February, Formlabs will also be running a giveaway on a Form 3+ Basic Package that includes the Form 3+ 3D printer, Build Platform, Resin Tank, Finish Kit, and one liter of Draft Resin, valued at $3,500. You can enter for a chance to win here.
Businesses and creators looking to invest in a new 3D printer to create models, prototypes, molds, and end-use parts will run into the question of which technology to use: fused deposition modeling (FDM) or stereolithography (SLA).
SLA was the first 3D printing technology created, and it has long been the preferred printing technology for professional designers and engineers. The SLA printing process uses an incredibly precise laser to cure liquid resin into the solid final part. Thanks to this precision, SLA prints can have incredibly fine detail, smooth finishes, and accurate sizing for machine parts and prototypes.
SLA printed parts come out dense, watertight, and isotropic, giving them structural integrity in a wider variety of applications. Those qualities combined with the precision of SLA-printed parts even allows them to be used in industrial applications.
There’s also a greater degree of flexibility available with SLA printing. Creators can use different SLA resins to produce hard or soft objects, use resins filled with additives like glass or wax, create either opaque or clear prints, and choose materials for their unique mechanical properties. There are also biocompatible materials available for SLA printing, allowing for customized healthcare products, like dental aligners or surgical planning tools.
There are some key ways that SLA printing differs from FDM, the other largely popular 3D printing technology. FDM printers deposit material in a melted form to build each layer of the print. Each line the printer deposits can be slightly rounded and may not always adhere perfectly to the layer beneath, creating an anisotropic structure. The resulting prints will show gradation between layers that can impact the aesthetics and functionality of the design.
The precision of FDM prints is also limited by the size of the extrusion nozzles and inaccuracies caused by the thermal expansion and contraction of the filament, so FDM printers are not as well suited for creating fine details on smaller designs. While FDM prints come out of the printer without requiring cleaning or post-curing, they may require support removal and sanding to remove any unwanted layer lines. This makes them better suited for quick mock-ups or for use in workflows that won’t involve considerable post-production work, which adds time and labor expenses that may negate the relative affordability of the printers and low cost of filament material.
So if SLA printers have so many clear advantages over FDM printers, why would anyone opt for an FDM printer? The answer is thatSLA printing technology hasn’t been as accessible for many companies. The large, industrial machines previously used for SLA printing were expensive, especially compared to many of the affordable FDM printers available on the market today.
A big factor in the price of SLA printers has been the expensive laser responsible for curing the resin. The resins can also be expensive, and the complicated process of shifting between print layers puts a strain on parts and could cause costly print failures.
But the relative inaccessibility of SLA printing has gradually been addressed by the introduction of desktop SLA printers from Formlabs. Formlabs has spent the last decade eliminating the prohibitive costs of SLA printing while simultaneously making the technology more versatile, reliable, and intuitive. These investments have culminated in the recently launched Form 3+ SLA printer.
The Form 3+ is a capable, fast, and reliable 3D printer for business applications. Its versatility allows users to employ it for rapid prototyping, end-use parts, model making, and more. The Form 3+ starts at $3,499 for the basic package.
The precision of the laser in the Form 3+ produces prints that require minimal post-processing. Beyond the smooth finishes of its prints, Formlabs’ software can automatically create support structures for each design and the laser can cure them in such a way that they break off easily and cleanly, further eliminating post-production work. The printer is backed by an ecosystem to improve and simplify the production pipeline, including automated washing and curing machines as well as a quick-release build platform.
The reliability of the printer and the quality of the prints can allow a business to save time and money on prototyping or designing custom parts. While the upfront cost may be higher than an entry-level FDM printer, the flexibility allows this printer to do more, and the reduction in post-production labor, print time, and print failures can outweigh the higher upfront costs. Ultimately, it’s an investment that makes sense for businesses looking to go from concept to final form quickly, precisely, and reliably.
If you think Formlabs’ Form 3+ may be right for your business or application, you can find out more about the printer here.
For the month of February, Formlabs will also be running a giveaway on a Form 3+ Basic Package that includes the Form 3+ 3D printer, Build Platform, Resin Tank, Finish Kit, and one liter of Draft Resin, valued at $3,500. You can enter for a chance to win here.
Sign up to get the BEST of Tom's Guide direct to your inbox.
Get instant access to breaking news, the hottest reviews, great deals and helpful tips.